Have you ever wondered why the operating and maintenance (O&M) costs of a project are surprisingly high compared to the initial design and construction expenses? This is a significant issue often overlooked by investors and project managers, yet it heavily impacts the long-term financial effectiveness of a project.
In reality, O&M costs can greatly surpass the initial design and construction expenses, not only creating financial pressure but also affecting project profitability. How can we address this issue?
This article delves deeper into operating and maintenance costs, comparing them with design and construction expenses, analyzing influencing factors, and exploring effective strategies to minimize these costs. Let’s look into optimizing design and construction processes to achieve a sustainable and cost-effective project!💡
Understanding Operating and Maintenance Costs
Definition of Operating Costs Operating costs refer to the total funds required to maintain the daily operations of a project or facility. This includes expenses like electricity, water, labor, consumables, and other routine costs.
Importance of Long-Term Cost Management Effective long-term cost management is essential for ensuring project sustainability and efficiency, supporting profitability, resource allocation, and extending asset life.
Comparison of O&M Costs with Design and Construction Costs Operating and maintenance costs can significantly impact a project's total budget. Often, O&M costs can be 3-5 times the initial design and construction expenses and may account for up to 80% of a building's total lifetime costs.
Components of Maintenance Costs
Maintenance costs include various elements, typically classified as follows:
Cost Type | Example |
Direct Costs | Materials, replacement parts |
Labor Costs | Maintenance staff wages, training |
Indirect Costs | Maintenance equipment, management software |
Contingency Costs | Reserve funds for unexpected incidents |
Understanding and effectively managing these elements can help optimize overall maintenance expenses. Next, we’ll compare operating costs with design and construction costs to get a comprehensive view of the project’s total cost.
Comparing Operating Costs with Design and Construction Costs
When assessing an overall construction project, comparing operating costs to design and construction expenses is a critical step. Let’s analyze this in more detail.
-
Impact on Total Project Budget
Operating and maintenance costs often constitute a large portion of a construction project’s total budget. This might surprise some, but in practice, we observe:- Operating costs can be 3-5 times the initial design and construction costs.
- Over a 30-year building lifespan, operating costs can represent up to 80% of total expenses.
-
Example from Real Projects
Phase | Cost (billion VND) | Percentage (%) |
Design | 10 | 5% |
Construction | 90 | 45% |
Operation (30 years) | 100 | 50% |
-
In this example, operating costs account for 50% of total expenses, five times the initial design costs.
Reasons for Higher Operating Costs
Several factors contribute to high operating costs:
- Extended Timeframe: Operations span the project’s entire lifecycle.
- Labor Costs: Staff is continuously required for operations and maintenance.
- Energy Consumption: Ongoing costs for electricity, water, gas, etc.
- Repairs and Replacements: Equipment needs regular maintenance and replacement.
Cost Ratio Analysis
When analyzing cost ratios, we typically see the following:
- Design Costs: 2-5% of the total cost
- Construction Costs: 20-30% of the total cost
- Operating and Maintenance Costs: 65-80% of the total cost
This demonstrates the importance of investing in high-quality design and construction to minimize future operating costs. Next, we’ll examine specific factors that impact operating and maintenance costs.
Factors Affecting Operating and Maintenance Costs
After understanding operating and maintenance costs and comparing them with design and construction expenses, let’s look at the primary factors influencing these costs. Identifying these factors provides a comprehensive view of the issue and helps in finding optimal solutions.
A. Operation and Maintenance Processes
Effective processes are crucial in determining costs. An efficient process can lead to significant savings, whereas an inefficient one may increase unnecessary expenses.
Factor | Cost Impact |
Maintenance Frequency | Directly affects labor and material costs |
Maintenance Methodology | Determines efficiency and execution time |
Asset Management | Impacts the lifespan and performance of equipment |
B. Environmental and Usage Conditions
The operating environment and usage practices greatly affect O&M costs:
- Harsh climates can accelerate degradation.
- Overuse or improper use increases repair frequency.
- Pollution and dust can impact equipment performance.
C. Choice of Materials and Equipment
The initial choice of materials and equipment has a lasting impact on O&M costs:
- Material Quality: High-quality materials generally last longer.
- Equipment Efficiency: Efficient equipment saves on energy costs.
- Compatibility: Easily maintained and upgradeable equipment reduces long-term costs.
D. Quality of Initial Design
Finally, the quality of the initial design greatly influences future operating and maintenance costs. A well-thought-out design considers factors like accessibility for maintenance, expandability, and the sustainability of the project.
By recognizing these influencing factors, it becomes clear that reducing O&M costs requires a comprehensive approach. Next, we’ll look at specific strategies to reduce these costs.
Strategies to Reduce Operating and Maintenance Costs
To optimize operating and maintenance costs, organizations should implement effective strategies. Below are some key measures:
A. Training Operations Staff
Investing in staff training is a crucial step in reducing long-term costs. Well-trained staff can:
- Detect and resolve issues early
- Operate equipment more efficiently
- Conduct preventive maintenance correctly
B. Planning Preventive Maintenance
Preventive maintenance helps prevent major issues and extends equipment lifespan. An effective maintenance plan includes:
- Scheduled periodic inspections
- Component replacements based on manufacturer recommendations
- Data analysis to predict maintenance needs
C. Implementing Smart Building Management Technology
Smart building management systems (BMS) can optimize operations and reduce costs:
Benefit of BMS | Description |
Energy Savings | Automatically adjusts HVAC and lighting systems |
Predictive Maintenance | Uses data to forecast maintenance needs |
Asset Management | Monitors equipment performance and lifespan |
D. Investing in Sustainable Design
Sustainable design can significantly reduce long-term operating costs:
- Use durable, low-maintenance materials
- Optimize energy efficiency
- Design flexibility for future upgrades
By implementing these strategies, organizations can greatly reduce operating and maintenance costs, while extending the lifespan and performance of facilities. Next, we’ll look at how to optimize the design and construction process to support these strategies.
Optimizing the Design and Construction Process
After understanding the importance of operating and maintenance costs, we need to consider how to optimize the design and construction process to reduce future costs.
- Evaluating Life Cycle Costs in Decision-Making
Life Cycle Cost Analysis (LCCA) is an essential method for making informed decisions during design and construction. LCCA helps us consider not only initial costs but also operating and maintenance costs throughout the project’s lifecycle.
Phase | Costs to Consider |
Design and Construction | Material, labor, and equipment costs |
Operation | Energy costs, regular maintenance |
Maintenance | Repair and component replacement |
End of Life | Demolition and recycling costs |
- Selecting Contractors with Long-Term Operations Experience
Choosing contractors with experience in long-term operations is essential for optimizing the design and construction process. These contractors can:
- Provide sustainable design solutions
- Use durable materials and long-lasting equipment
- Integrate energy-saving solutions
- Using Building Information Modeling (BIM)
BIM is a powerful tool that optimizes the design and construction process by allowing:
- Conflict detection and resolution before construction
- Energy performance simulations
- Preventive maintenance planning
- Incorporating Operational Considerations in the Design Stage
Finally, integrating operational considerations into the design stage is key to reducing future operating and maintenance costs. This includes:
- Designing accessible spaces for maintenance
- Choosing efficient HVAC systems
- Integrating smart building management systems
By applying these methods, we can ensure that the project is not only functional and visually appealing but also cost-effective throughout its entire lifecycle.
This section emphasizes strategies for reducing costs through sustainable design, preventive maintenance, and smart technology, as well as the benefits of lifecycle cost analysis in decision-making.
Tags
Related news
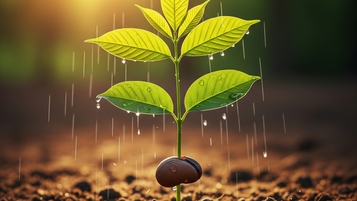
Dependent Origination & Cause-and-Effect: A Rooted Path to Business Growth
In a fast-changing and competitive world, running a company today requires more than just technical skills and business strategies. It...
View detail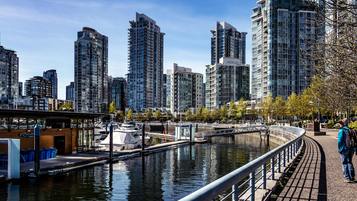
Creating a Sustainable Office Space: A Step-by-Step Guide
Have you ever wondered if your office could contribute to a greener future? 🌿In an era of increasing environmental awareness,...
View detail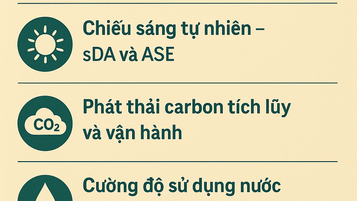
Sustainable Building Design: 5 Metrics Architects Need to Know
Introduction As global energy codes become increasingly stringent, architects must prepare for a wide range of challenges. The first step...
View detail